Crude oil is less useful unless subjected to refining processes. The refining of petroleum involves subjecting the crude oil feedstock to a series of physical and chemical processes to obtain varieties of products that are valuable for energy generation, petrochemical products and lots of consumer products such as polymers, detergent, pharmaceuticals, pesticides among others.
The first process is the physical process which includes distillation of the constituents of the crude oil feedstock and isolating different fractions. This does not change the chemical composition of the crude oil components.
The other is the chemical conversion processes which are either thermal or catalytic conversion processes. It may be cracking or reforming/isomerization process. This section will focus on only the physical refining processes.
Physical Refining Processes
The crude oil refining process start with removal of salt and water from the raw crude oil from the exploration well which is then followed by the distillation processes (atmospheric and vacuum distillation.
Desalting and Dewatering
The very first step in the separation of petroleum into its various constituents is the cleaning of the crude oil by desalting and dewatering it. The aim is to remove water and brine that do always accompany crude oil after exploration from its reservoir into the wellhead.
Petroleum upon recovery from the reservoir contains a number of components such as gases, water, and mineral salts/dirt. The pre- treatment operations desalting and dewatering are applied to the crude oil prior to sales/transportation and refining.
Read Also : Mechanisms of Petroleum Migration and Petroleum Occurrence
This quality improvement is require for the shipping/pipeline transportation of the crude to guide against corrosion of the vessels. It is also required for crude oil buyer’s specification to guide against causing operating problems such as equipment plugging and corrosion, catalyst deactivation during refinery processing.
Desalting involves water washing operation. The process involves the feeding of unrefined crude contains water and dirt using a pump through a heater.
The process water is added with another pump and an emulsifier, to aid the mixing and water-washing, before the mixture is charged into an electrostatic desalting unit (gravity settling tank).
In the tank, the electric power breaks the emulsion and the water separate from the crude oil. The water washing removes much of the water-soluble minerals and entrained solids and the water settles at the lower part of the tank being denser than the crude oil. The desalted water is collected at the upper part of the tank.
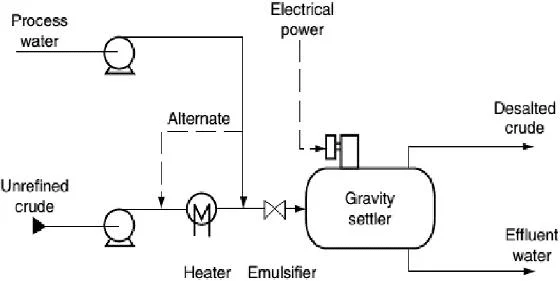
Atmospheric Distillation
After desalting and dewatering, the desalted crude oil is charged as feed into the petroleum distillation unit. A fractional distillation tower is used as modern-day refinery. This tower brings about efficient fractionation (separation).
The feeding process of the petroleum into the distillation tower involves pre-heating by flow- through pipes (i.e. pipe still heater or pipe still furnace) arranged within a large furnace. The heated crude enters into the fractional distillation tower which forms an essential part of the distillation unit.
The pipe still furnace performs that heating of the feed to a predetermined temperature at which each fraction in the feed changes into vapour. The vapour is held under atmospheric pressure in the furnace pipe until it is discharges as feed stream into the fractional distillation tower.
The feed pass up inside the tower is then fractionated according to the boiling temperatures into gas, gasoline, heavy naphtha, kerosene and gas oils.
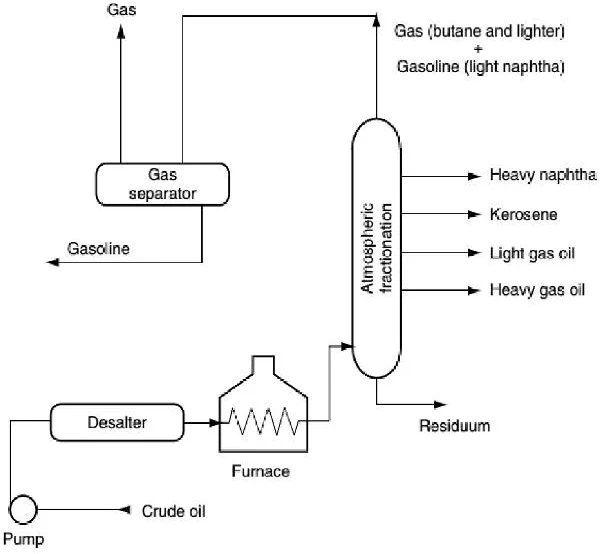
Figure: Flow sheet of Atmospheric Distillation Process Crude Oil (Speight 2006)
Vacuum DistillationProcess
The lower boiling fraction (Residuum) from the atmospheric distillation is used as the feedstock for the vacuum distillation.
Vacuum distillation evolved because of the need to separate the less volatile products, such as lubricating oils, from the petroleum without subjecting the crude oil to high temperature that can lead to cracking conditions.
If atmospheric distillation is used, the heaviest boiling fraction obtainable without cracking is limited by the temperature to 350 oC.
Vacuum distillation process is therefore a more recent technique and has since been widely used in petroleum refining to address the drawback of cracking at high temperature in atmospheric distillation.
Read Also : Roles of Producers and Corporations in Waste Management
Vacuum distillation operates in a way similar to atmospheric distillation with an additional feature of a vacuum which create a pressure of 50 to 100 mmHg (¼ of the atmospheric pressure 760 mmHg).
A vacuum tower is often of larger diameter (14 m) than the atmospheric units so as to minimize pressure fluctuation in the units.
As a result of the operation of vacuum, heavy gas oil is obtainable in the distillation tower at temperatures of about 150 oC and lubricating oil at temperature range of 250 oC to350 oC.
In the vacuum tower, the feed and residue temperatures should be kept below the temperature of 350 oC, to avoid cracking. The vacuum residuum is often applied as asphalt.
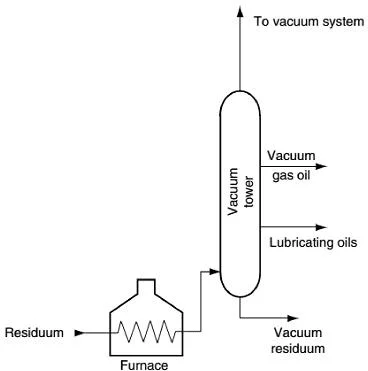
Figure: Flowsheet of Vacuum Distillation Process Crude Oil (Speight 2006)