Waste Minimisation Technology
Waste minimisation is any action that reduces the amount and/or toxicity of waste produced by a process. The most desirable method of waste minimisation is source reduction (minimising quantity of waste produced at source), which reduces the impact of chemical wastes on the environment to the greatest extent. This activity reduces or eliminates the generation of waste at the source.
The next most desirable approach is waste minimisation through recycling. When a waste material is used for another purpose, treated and reused in the same process, or reclaimed for another process, this is called recycling.
The last minimisation method is treatment. The most common treatment that can be performed is elementary neutralisation (minimising or eliminating the corrosive or toxic chemical in waste).
Other kinds of treatment may involve chemical, physical or biological methods. Other methods include waste substitution, which involves replacing one material with another in a process of production.
Example includes substituting hazardous material with non-hazardous ones to minimise the toxic effect of waste produced. For example, Alconox may be used in the cleaning of glassware instead of chromic acid based cleaners. Modification of procedures, processes or equipment can also lead to waste minimisation.
In laboratories or factories where high volumes of spent solvents are generated, distillation would provide a cost-effective means of re-using these solvents. Good production practices such as computer modelling and small-scale experiments can minimise waste.
Generally waste minimisation reduces the quantity and/or hazardousness of waste generated by a process at source or at any other point of generation, recycling at source (at the factory or at any other point) of waste generated and undertaking appropriate treatment of waste to reduce its harzardousness.
As shown by the figure, waste reduction is achieved through product modification or process modification while waste treatment reduces the hazardousness of waste. The examples below clearly illustrate these.
Waste Recycling and Conversion Technology
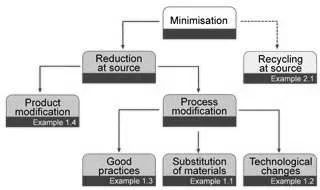
Example1:Substituting raw materials with less pollutant ones
A company that manufactures metal parts by means of precision cutting techniques decided to replace the chlorinated solvent used in the degreasing process with a water-based alkaline detergent.
This measure required the installation of two cleaning machines incorporating an oil and dust separation system in order to prolong the useful life of the bath. This measure enabled the elimination of the consumption and subsequent management of the chlorinated solvent (from 9.6 tons/year to 0 tons/year).
Example 2: Introducing new, more efficient technologies into the production process
A company that repairs and cleans merchant ships uses spray guns and solvent-based paint in the hull painting process.
Electrostatic paint guns, which increase the application capacity of the paint, were installed and a reduction in the consumption of paint (38%), solvent (2.6%) and packaging waste (7.6%) was achieved.
Read Also : Concept and Definition of Biotechnology
The payback period, taking into account the investment (€41,000) and the annual savings on raw materials and waste management (€1,105,032.12), was 1 month.
Example3: Applying good environmental practices
A metal processing company systematically cleaned the die by hand before verifying its state and preparing it for new operations. The cleaning process was carried out by submerging the die in a bath of 30% sodium hydroxide, which subsequently had to be managed as liquid waste.
The good practice that was applied consisted in introducing a new procedure to control the state of the die, preventing unnecessary cleaning.
This good practice reduced the generation of liquid waste by 40% (41 tons/year), and it also had an effect on the availability of personnel, as time could be spent on other activities.
Example 4: Developing new products and applying improvements to already existing ones, integrating environmental criteria (ecodesign)
A company that manufactures plastic components for the automobile industry has developed a new method of joining or welding parts. The new system involves the use of a system of joining by vibration or ultrasound.
Using this ecodesign method, the company has minimised manufacturing waste and made a significant reduction in the energy consumption associated with this process.
Example 5: Once the waste has been generated, trying to recycle it at the source
A company that manufactures interior modules for vehicles uses hydraulic oil to operate its plastic injection machines. It installed filters in the oil circuits in order to prolong their useful life by eliminating impurities that would accumulate, thus minimising waste.
Thanks to this measure, oil changes are now carried out every 7 years instead of every year, representing a reduction of 16.72 tons/year. This also led to a reduction of 21.3 tons/year of oil waste, representing a reduction of 60%.
Organic fertilizer and bio-fuel production
Composting is a natural process that turns organic material into a dark rich substance known as compost or humus under the action of microorganisms. Improved composting through biotechnology is now being used to produce organic fertilizer which is being marketed around the country under different brand names.
Factories for organic fertilizer production now exist in Ibadan, Minna, Akure, Lagos etc. Modern biotechnology methods of organic fertilizer production include:
Engineered landfill
Biodigester/bioreactor
The engineered landfill involves anaerobic digestion of municipal wastes in containment facilities. The main constituents of bio-digesters are pre-fabricated facilities mounted above the ground shelter.
The bio-digester tank is a cylindrical structure with the provision of inlet for waste supply and out let for biogas. Temperature in the bio – digester is maintained between 5-30 ˚C.
A consortium of anaerobic bacteria converts the organic waste into methane, carbon dioxide and black soil. They also eliminate the smell of night soil, the disease causing organisms in the night soil and the solid matter totally.
On dry weight basis, 90 per cent of the solid waste is reduced. The gaseous effluent (biogas) is continuously let off to the atmosphere. The biogas can be collected and used for various energy incentive activities like cooking, water and room heating.
Liquid effluent can be drained to any surface or soak pit without any environmental hazards. Bioreactors facilities mounted underground is known as bioreactor. Both are very efficient, easy to maintain and environmentally friendly.

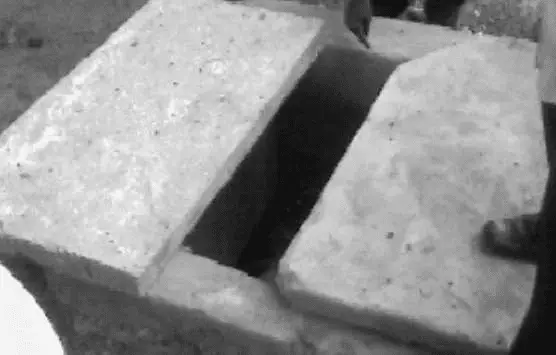
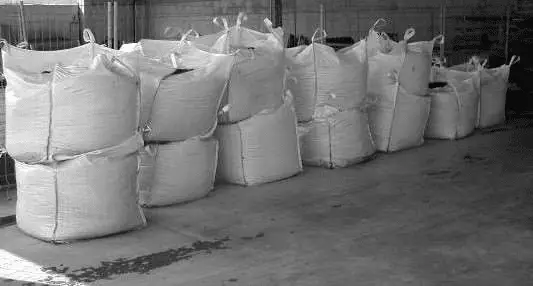
Biotechnology is fast optimising performance and efficiency of bio- digesters and bioreactors by developing more efficient microbes and enzymes not only to make bio-digesters work better but faster too.
The most typical example is the development of Hydro-Bio-digesters (HBD- O), a combination of all natural bacteria, lab-grade purified enzymes with micro and macronutrients.
HBD-O bacteria and enzymes target biodegradable materials in bio-digester facilities and by out competing the natural occurring bacteria for resources available, odor causing bacteria die off and thus the objectionable smell is eliminated.
HBD-O are so prolific they multiply by double every 15-20 minutes. If you start out with one cell in fifteen minutes you have two and so on. In 8 hours you will have 17-million and in twenty-four hours you have a 1 with one hundred and twenty six zeros behind it. They simply outnumber the bacteria present in the system. HBD-O was developed by Hydro Engineers of United States of America.
There are over 3,000 known bacterial strains in HBD-O. The bacteria and enzymes are selected for their ability to aggressively breakdown the targeted substrate. Process of selection involves first selecting only facultative strains that can operate in aerobic (with oxygen) or anaerobic (oxygen depleted) situations.
They are, however, most effective in an aerobic state working 5-7 times faster than in anaerobic condition. They are also resistance to high and low pH, chemical shock and temperature.
HBD-O can tolerate a ph of 4.5 to 9.5 without dying off, but, the closer to neutral pH of 7 the better. They are resistant to disinfectants like chlorine up to 150 ppm and remain active in temperature ranges of 10- 60˚C. HBD-O are not genetically-engineered but are all naturally occurring strains.
They are marketed in two forms, liquid and dry formulars each at a concentration of 1.22 trillion cells Kg of active cell count for two years. Once stabilized in a liquid that does not break the micro encapsulation process HBD-O remains 100% viable with a cell count of 119 billion per litre for one full year.
Dosing rate of HBD dry formula is used for seed dosing (initial propagation) at a rate of 1 Kg pound per 14000 litres of wastewater. The product is simply mixed in warm (not hot) water and evenly introduce into all water holding tanks within the system. HBD Liquid can be automatically dosed into the water.
Application rates are 85 g per 4000 litres of water per day. HBD-O enzymes and microorganisms work in concert to digest long chain hydrocarbons, light fuels, sludge, fats, and grease.
HBD-O’S targeted enzymes breakdown the substrate for digestion by the bacteria. In high hydrocarbon applications nutrients supplement the bacteria’s diet. The result is a significant reduction of BOD/COD and TSS. The byproducts produced from this biological transformation are absolutely harmless and “stink” free – only carbon dioxide and water remain.
They propagate the bottom solids reducing them and liberating oils and grease into the water column for digestion. Floating fatty crust is broken down and eliminated.
The bacteria take up residence in the entire system constantly eating it clean, coalescing plates are kept clean, pipes and valves don’t plug up. Many other genetically-engineered bacteria working in similar way are available in the market.
In summary,two important emerging methods were described in this article. These included waste minimisation and waste to wealth technologies. Waste minimisation is achieved through the use to technologies that lead to waste recycling and waste reduction while waste to wealth technologies involves the production of organic fertilizers and bio-fuel which is mainly methane.
Both waste recycling and waste reduction involve either process or product modification or both. Modification may involve change in the raw materials used or change in the process of production to minimise the quantity waste produced and to reduce the hazardousness of the waste.
Production of organic fertilizer and bio-fuel employ the principle of composting using either genetically-engineered microbes or genetically-modified enzymes in well-designed facilities known as bio-digester (mounted above the surface) or bioreactor (mounted underground).
Read Also : The Two (2) Main Modern Waste Management
Examples were given of companies that now manufacture and market either genetically- engineered or biotechnologically optimised bacteria for this process.
The emerging waste management methods are directed towards waste minimisation involving waste recycling, re-use and reduction at source.
Waste minimisation is based on process and product modification as well as waste treatment to reduce the hazardousness of waste. These may involve change in the raw materials used or development of technologies that reduces amount of waste generated.
Waste conversion processes for the production of bio-fuels and organic fertilizer process uses the principle of composting involving well designed facilities. The two common of such facilities are the bio-digesters and bioreactors.
Bio- digester facility is usually mounted above the ground while bioreactor facilities are mounted underground. Each facility, which is usually cylindrical in shape, is designed such that waste materials are loaded from one end and gas released at the other.
The methane gas released may be collected and used for heating, lighting or electric generation. Black soil left in the facilities after decomposition by microorganisms is used as organic fertilizer.
The role of either genetically-engineered microbes or biotechnologically optimised bacteria and enzymes in bio- digester/bioreactor technologies was also described. In the next unit, you will learn how similar biotechnological methods are applied to pest and disease control.