Turning wastes into battery casings means instead of throwing away the plastic containers, they can be used to make coverings for batteries. This is a good thing because it helps the environment and saves resources.
When we throw away plastic containers, they often end up in landfills. These landfills can harm the environment because plastic takes a long time to break down. But if we turn these containers into battery casings, we can reduce the amount of waste going into landfills.
Battery casings are important because they protect the batteries inside. If the casing is made from plastic containers, it still does the job of protecting the battery, but it also helps to recycle the plastic. This is called recycling, and it’s a way of using things again instead of throwing them away.
By recycling plastic containers into battery casings, we also save resources. Instead of making new plastic for the casings, we can use the plastic that’s already been used once. This saves energy and raw materials.
Another good thing about turning plastic containers into battery casings is that it can create job opportunities. People can work in factories that recycle the plastic and turn it into casings. This means more jobs for people in the community.
Overall, converting Plastic Containers (PP) Wastes into Battery Casings is a great idea. It helps the environment by reducing waste in landfills, saves resources by reusing plastic, and creates job opportunities. It’s a win-win situation for everyone.
Read Also: Practical Steps to Convert Plastic Containers (PVC) Wastes into Fencing
Types of Recyclable Plastic Containers (PP) Wastes and their Uses
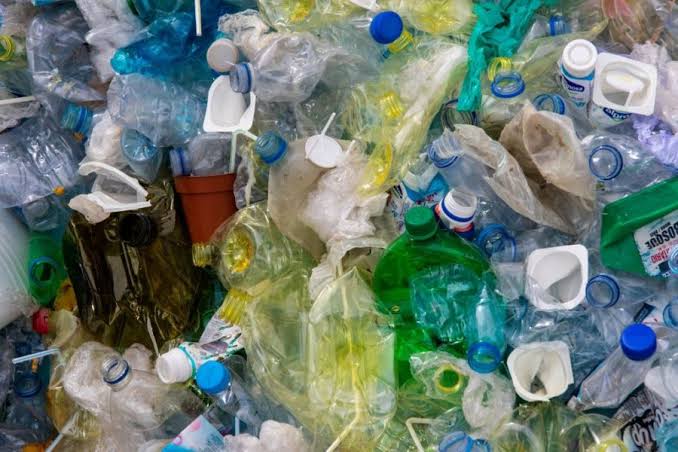
Recyclable Plastic Containers (PP) come in various types, each serving different purposes. Here are some common types and their uses:
1. Food Containers: These are often used for packaging food items like yogurt, margarine, or deli meats. Once recycled, they can be turned into battery casings as mentioned earlier.
2. Beverage Bottles: Plastic bottles used for beverages like water, soda, or juice are typically made from PP plastic. After recycling, they can be transformed into battery casings or even new plastic bottles.
3. Cosmetic and Personal Care Containers: Items like shampoo bottles, lotion containers, and makeup jars are often made from PP plastic. When recycled, they can be used to create a variety of products, including battery casings.
4. Household Product Containers: Cleaning product bottles, laundry detergent jugs, and dish soap containers are commonly made from PP plastic. Once recycled, they can be repurposed into battery casings or other household items.
5. Takeout Containers: Many takeout containers, such as those used for soups, salads, and leftovers, are made from PP plastic. Recycling them can result in the creation of battery casings or new containers for food packaging.
6. Medical Supplies Packaging: Some medical supplies, like pill bottles and medicine containers, are made from PP plastic. Recycling them can lead to the production of battery casings or other medical-related products.
These are just a few examples of recyclable Plastic Containers (PP) and their potential uses after recycling. By properly recycling these items, we can reduce waste, conserve resources, and contribute to a more sustainable future.
How to Convert Plastic Containers (PP) Wastes into Battery Casings
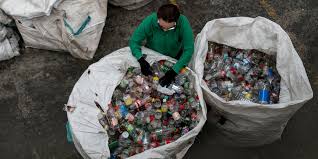
Converting Plastic Containers (PP) Wastes into Battery Casings involves several steps:
1. Collection: First, plastic containers made from PP plastic need to be collected. This can be done through community recycling programs, waste management services, or by individuals separating their recyclables at home.
2. Sorting: Once collected, the plastic containers are sorted based on their type and quality. This ensures that only PP plastic containers are used for making battery casings.
3. Cleaning: The sorted plastic containers are then cleaned to remove any labels, residues, or contaminants. Clean plastic ensures a higher quality end product.
4. Shredding: After cleaning, the plastic containers are shredded into small pieces. This increases the surface area and makes it easier to melt the plastic during the next step.
5. Melting and Molding: The shredded PP plastic is melted down and then molded into the shape of battery casings. This process can be done using injection molding machines, where the melted plastic is injected into molds to form the desired shape.
6. Cooling and Finishing: Once molded, the battery casings are cooled down to solidify them. They are then inspected for any defects and trimmed or finished as necessary to ensure they meet quality standards.
7. Packaging: Finally, the finished battery casings are packaged and distributed for use in battery manufacturing.
By following these steps, Plastic Containers (PP) Wastes can be effectively converted into Battery Casings, contributing to waste reduction and resource conservation efforts.
The Benefits of Converting Plastic Containers (PP) Wastes into Battery Casings
Converting Plastic Containers (PP) Wastes into Battery Casings offers several benefits:
1. Waste Reduction: By repurposing plastic containers into battery casings, we reduce the amount of plastic waste going into landfills or ending up in the environment. This helps to mitigate pollution and environmental degradation.
2. Resource Conservation: Recycling plastic containers conserves valuable resources by reducing the need for virgin materials in the production of battery casings. This helps to preserve natural resources such as oil, which is a primary component of plastic production.
3. Energy Savings: Recycling plastic requires less energy compared to producing new plastic from raw materials. Converting PP plastic containers into battery casings consumes less energy, leading to overall energy savings and a reduction in greenhouse gas emissions.
4. Circular Economy: Converting plastic waste into useful products like battery casings promotes a circular economy where materials are reused and recycled, rather than disposed of after a single use. This contributes to a more sustainable and environmentally friendly approach to resource management.
5. Job Creation: Recycling initiatives, including the conversion of plastic waste into battery casings, create employment opportunities in various sectors such as waste collection, sorting, processing, and manufacturing. This contributes to economic development and supports local communities.
6. Reduced Environmental Impact: By utilizing recycled plastic for battery casings, we lessen the environmental impact associated with traditional plastic production, such as habitat destruction, pollution, and carbon emissions. This helps to protect ecosystems and biodiversity.
7. Product Innovation: Converting plastic containers into battery casings encourages innovation in recycling technologies and product design. This may lead to the development of new, more sustainable materials and processes, further enhancing environmental sustainability.
Overall, the benefits of converting Plastic Containers (PP) Wastes into Battery Casings extend beyond waste management, encompassing environmental protection, resource efficiency, and socio-economic development.
Read Also: How to Convert Plastic Containers (LDPE) Wastes into Landscaping Tiles
The Uses and Benefits of Recycled Battery Casings
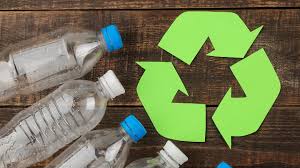
Recycled Battery Casings have several uses and benefits:
1. Environmental Conservation: Using recycled battery casings reduces the demand for new plastic, thereby conserving natural resources and reducing environmental degradation associated with plastic production.
2. Waste Reduction: By repurposing materials that would otherwise end up in landfills, recycled battery casings help to minimize waste and promote a circular economy where resources are reused and recycled.
3. Energy Savings: Recycling materials like plastic to make battery casings consumes less energy compared to producing them from raw materials. This leads to energy savings and a reduction in greenhouse gas emissions.
4. Cost Savings: Manufacturing battery casings from recycled materials can be more cost-effective than using virgin materials, contributing to cost savings for manufacturers and consumers alike.
5. Product Performance: Recycled battery casings can offer comparable performance to those made from virgin materials. They are durable, lightweight, and resistant to corrosion, providing adequate protection for batteries.
6. Regulatory Compliance: Many jurisdictions have regulations and standards in place promoting the use of recycled materials in product manufacturing. Utilizing recycled battery casings helps companies comply with these regulations and demonstrate their commitment to sustainability.
7. Consumer Appeal: As environmental awareness grows, consumers are increasingly looking for products made from recycled materials. Using recycled battery casings can enhance a company’s brand image and appeal to environmentally conscious consumers.
8. Job Creation: Recycling initiatives, including the production of recycled battery casings, create employment opportunities in waste management, manufacturing, and related industries, contributing to economic development and job creation.
Overall, the uses and benefits of recycled battery casings extend beyond environmental conservation to encompass economic, social, and regulatory aspects, making them a valuable and sustainable choice for battery packaging.
The Challenges of Converting Plastic Containers (PP) Wastes into Battery Casings and their Solutions
Converting Plastic Containers (PP) Wastes into Battery Casings comes with its own set of challenges, but there are solutions to overcome them:
1. Contamination: One of the main challenges is contamination of the plastic containers with other materials, such as food residue or non-recyclable plastics. This can affect the quality of the recycled material and the final battery casings.
Solution: Implementing effective sorting and cleaning processes can help remove contaminants from the plastic containers before they are recycled. Education and awareness campaigns can also encourage consumers to properly dispose of their plastic waste.
2. Quality Control: Ensuring the quality of the recycled plastic is crucial for producing high-quality battery casings. Variations in the composition and properties of recycled plastic can affect the performance and durability of the casings.
Solution: Implementing strict quality control measures throughout the recycling process, including sorting, cleaning, and manufacturing, can help maintain consistency and reliability in the production of battery casings. Investing in advanced technology and equipment for material testing and analysis can also improve quality control.
3. Market Demand: The demand for recycled battery casings may fluctuate depending on market trends, consumer preferences, and regulatory requirements. Limited market demand can pose a challenge for recycling facilities and manufacturers.
Solution: Collaborating with battery manufacturers, retailers, and government agencies to promote the use of recycled materials in battery casings can help create a steady market demand. Offering incentives or subsidies for businesses that use recycled materials can also stimulate demand and support the recycling industry.
4. Logistics and Transportation: Collecting and transporting plastic containers from various sources to recycling facilities can be logistically challenging and expensive, especially in rural or remote areas.
Solution: Developing efficient collection and transportation networks, such as centralized collection points, mobile recycling units, or partnerships with local businesses and municipalities, can help streamline the logistics and reduce costs. Investing in eco-friendly transportation methods, such as electric vehicles or biodiesel trucks, can also minimize environmental impact.
5. Technological Limitations: Some recycling technologies may have limitations in processing certain types of plastic containers, especially those with complex shapes or multi-layered structures.
Solution: Investing in research and development to improve existing recycling technologies or develop new ones tailored to handle diverse types of plastic containers can expand the capabilities of recycling facilities. Collaboration with academic institutions, technology providers, and industry partners can facilitate innovation and knowledge sharing in the field of plastic recycling.
By addressing these challenges with proactive solutions, converting Plastic Containers (PP) Wastes into Battery Casings can become more efficient, cost-effective, and sustainable, contributing to the circular economy and environmental conservation efforts.
Frequently Asked Questions (FAQs) About How to Convert Plastic Containers (PP) Wastes into Battery Casings
1. Q: How are plastic containers (PP) recycled into battery casings?
A: Plastic containers (PP) are collected, sorted, cleaned, shredded, melted, molded into battery casing shapes, cooled, inspected, and finished before being packaged for distribution.
2. Q: What types of plastic containers (PP) can be used for making battery casings?
A: Various types of plastic containers made from PP plastic can be used, including food containers, beverage bottles, cosmetic and personal care containers, household product containers, takeout containers, and medical supplies packaging.
3. Q: What are the benefits of converting plastic containers (PP) wastes into battery casings?
A: The benefits include waste reduction, resource conservation, energy savings, circular economy promotion, job creation, reduced environmental impact, and product innovation.
4. Q: How does converting plastic containers (PP) wastes into battery casings contribute to environmental conservation?
A: It reduces the amount of plastic waste going into landfills, conserves natural resources by reusing materials, minimizes energy consumption, and promotes a circular economy where materials are reused and recycled.
5. Q: Can recycled battery casings perform as well as those made from virgin materials?
A: Yes, recycled battery casings can offer comparable performance to those made from virgin materials. They are durable, lightweight, resistant to corrosion, and meet quality standards.
6. Q: What challenges are involved in converting plastic containers (PP) wastes into battery casings?
A: Challenges include contamination, quality control, market demand fluctuations, logistics and transportation issues, and technological limitations.
7. Q: How can these challenges be overcome?
A: Solutions include implementing effective sorting and cleaning processes, implementing strict quality control measures, collaborating to stimulate market demand, developing efficient logistics networks, and investing in research and development for improved recycling technologies.
Read Also: The Importance and Uses of Chicory